Where tracks to safety begin
Rail – those polished parallel ribbons of steel – captures the imagination. Gazing into the horizon, the narrowing lines seemingly go on forever.
But where does the life of rail itself begin? It starts as hot rolled carbon steel strong enough to withstand the impact of thousands of tons of a train’s weight. Three types of U.S.-made rail are used at BNSF on our mainlines: 115-, 136- and 141-pound rail (pounds per yard), depending on the tonnage that moves on the line. The rail is uniformly shaped with a special design to support and guide the train’s flanged wheels as it heads down the track.
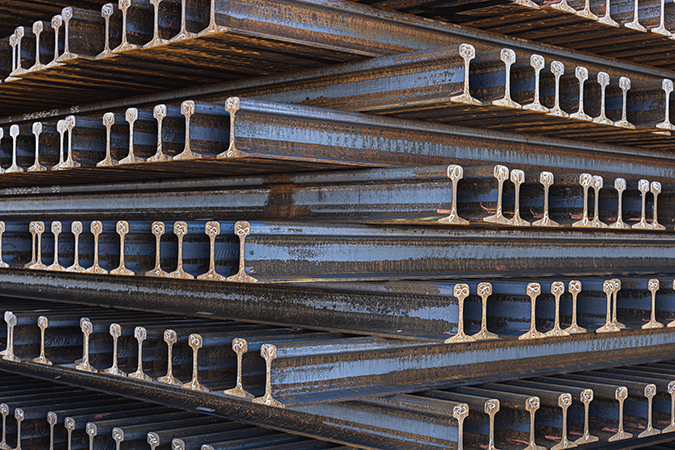
Before rail becomes part of the track, it is manufactured by steel rail producers that send the sections to us as 80-foot “sticks.” These arrive by train on flat cars at one of our three rail complexes: Laurel, Montana; Pueblo, Colorado; and Springfield, Missouri. Here they are offloaded and stored to be turned into sections up to 1,680-foot-long (nearly one-third of a mile) of continuous welded rail (CWR).
CWR—or ribbon rail—has fewer seams that make for a much smoother, safer ride, need less maintenance and allow trains to travel at higher speeds. Before the invention of CWR, rail was jointed, meaning bolted together, which meant speeds were restricted. Jointed rail is primarily used today within rail yards, where trains are required to move slowly.
To turn the steel sticks into CWR, the complexes operate in assembly-line fashion to weld the pieces together using a fusion welding process.
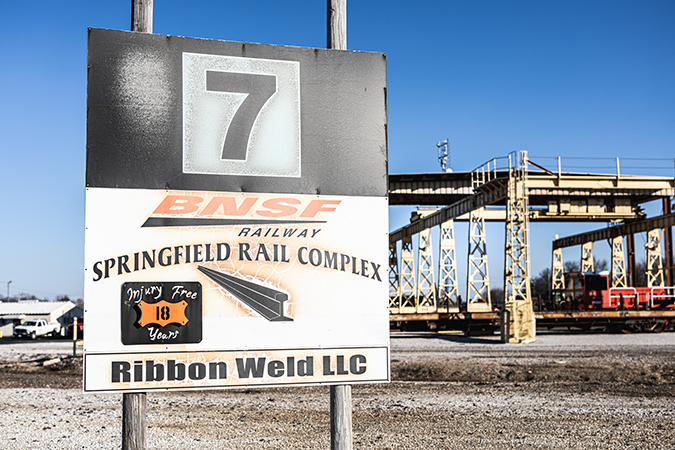
Here’s a day-in-the-life look at how this unique work is done at our Springfield facility, which has gone more than 18 years without an injury.
With 10-hour days, four days a week, each starts early with a briefing – about the work ahead and how to perform it safely. Conversations cover the weather, exposures, risks and eliminating those. “Safety is always first, above production,” Complex Manager Mark Neufeld said. “We have one pace and that’s to get home safely.”
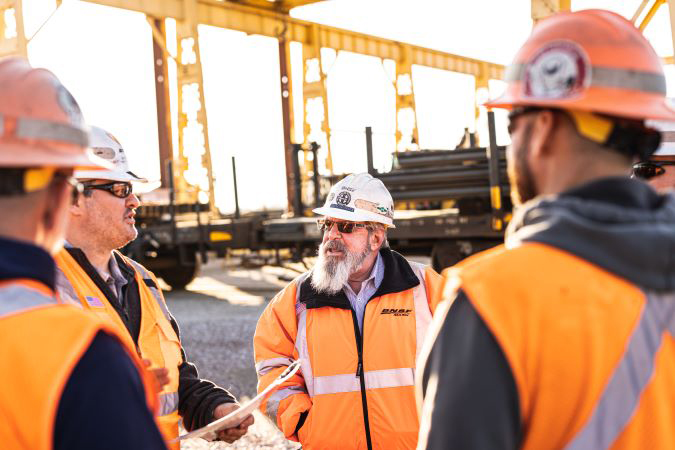
Neufeld and his team of 15 know well in advance how much CWR they need to produce to supply the rail production gangs. “Our busiest time starts with the new year as the production gangs start up their work,” Neufeld said. “Our production work will have begun the previous October so that the rail is where it needs to be when the gangs arrive.”
Springfield supplies CWR for gangs working in the southern portion of our network as they either replace or add track. Sometimes it’s needed quickly, for example, following a derailment or weather event.
To begin the production, the “stick” of steel is lined up into an automated conveyer that moves the rail into the welding machine. A strong electric current through the touching ends of two unjoined rails raises the temperature of the rail in the welder. The ends become red hot due to electrical resistance and are pressed together forming a strong weld.
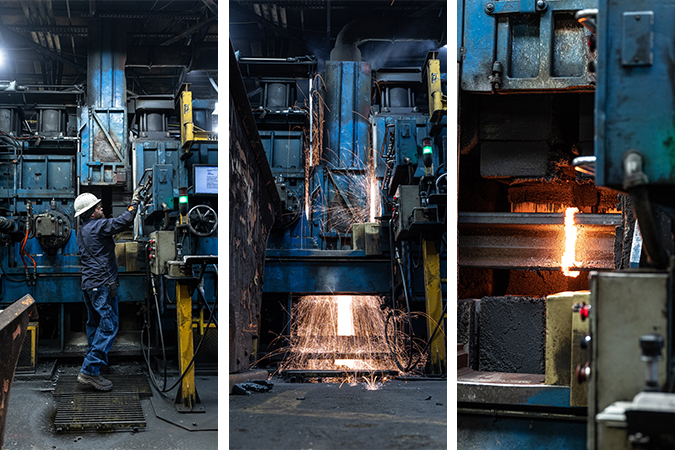
After the weld is completed, with the new piece of rail aligned horizontally and vertically, the slag – or excess around the weld – is sheared off. In the meantime, the next stick is moving forward in the machine to continue the process. It will take 18 sticks to make one piece of CWR.
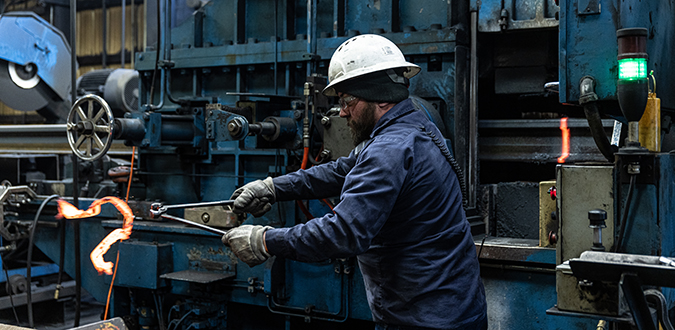
As the new piece of CWR moves down the line, the next part of the process is grinding. “We want to remove all sharp edges on the tops and sides of the rails. The same is done for the bottom of the rail. This ensures there are no impurities in the rail,” Neufeld said.
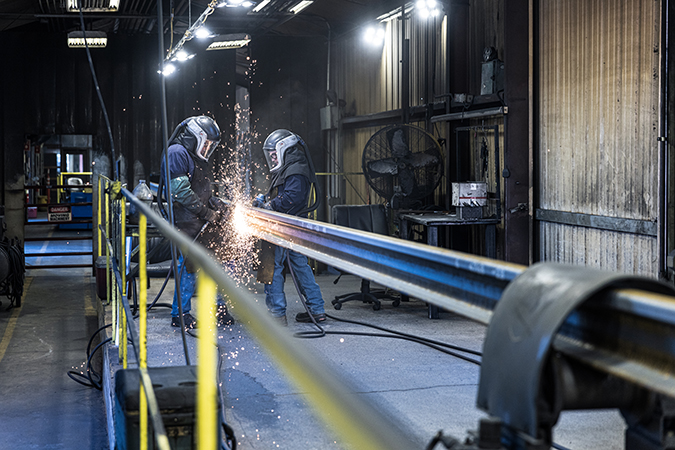
Once all sides of the rail have been through the grinding process, a press operator uses a machine to make sure the rail, which is still warm, is straight and level.
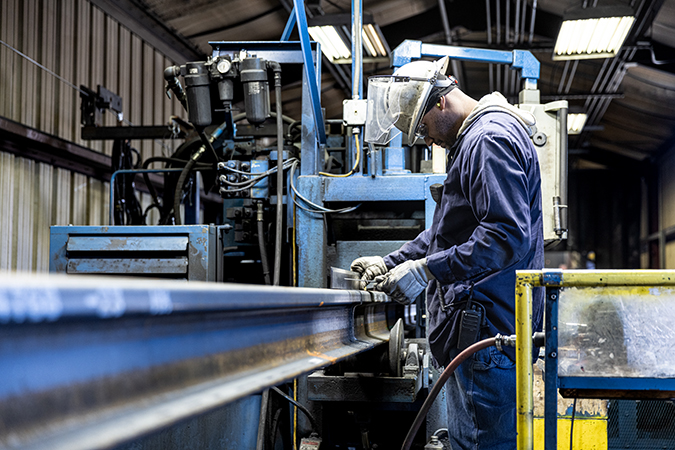
As the CWR leaves the inside line, it is loaded on a special train to carry it to the job site. This train is designed to carry many segments of rail that are placed so they can slide off their racks to the rear of the train and be positioned alongside the ties for installation.

With major capital and maintenance projects underway now the CWR will help us to safely and reliably operate our network while supporting the needs of our customers. Nearly 350 miles of rail will be replaced in 2023 – much of it with the CWR made at Springfield, where job safety and quality of the welded rail are paramount.
Or as Neufeld said of his team’s work ethic and safety-mindedness: “We believe that our most important day is today.”